Een schat aan informatie is te vinden in het boek "Rotterdam Hofplein - Den Haag - Scheveningen Kurhaus" van J.F.Smit, "Hoe het spoor elektrisch werd" ISBN 90-71082-09-1 (1989), een "must-have" voor de echte spoorliefhebber.
De bouw van dit model werd ook gepubliceerd in "De Modelbouwer" van augustus 2019
ZHESM
In 1908 reed de eerste elektrische trein in Nederland op de lijn van Rotterdam Hofplein naar Scheveningen, geëxploiteerd door de Zuidhollandse Elektrische Spoorweg Maatschappij ZHESM. Van deze trein ken ik geen commercieel verkrijgbaar model dus dan maar zelf gebouwd. Met CNC-frees techniek werden alle vormdelen gemaakt.
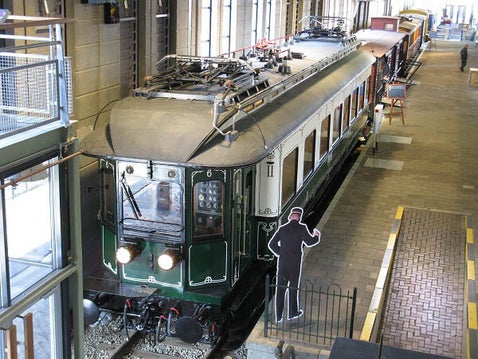
Toen de plannen tot zelfbouw ontstonden ben ik eerst het groot-bedrijf voorbeeld in het Spoorwegmuseum in Utrecht gaan bekijken en ook beluisteren wat de suppoost ter plaatse er over wist te vertellen. Wat me vooral is bijgebleven is dat hij me op het hart drukte er vooral drie te bouwen want deze treinen reden meestal in "rotten van drie", twee motorwagens met daartussen een bijwagen.
Motorwagen mBC
Motor draaistel
Gebruik is gemaakt van een Tenshodo WB-28.7 draaistel. De oorspronkelijke wielen en assen voor een 2-rail systeem werden vervangen door Märklin assen. De tandwielen werden overgezet op deze Märklin assen. Het motorhuis is exact 14 mm breed en om ruimte te maken voor Märklin wielen die ook precies 14mm apart staan werd aan weerszijden een paar tienden mm weg gefreesd van het huis. De contactveren voor het 2-rail systeem werden verwijderd.
Op de draaibank werd een 0,4 mm diepe groef in de Märklin wielen gefreesd waarin een antislip bandje werd ge[laatst. De assen met gemodificeerde wielen werden vervolgens terug geplaatst in het motorhuis.
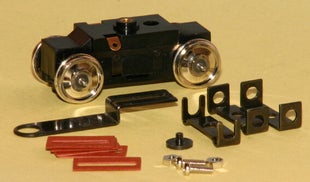
Tenshodo motordraaistel
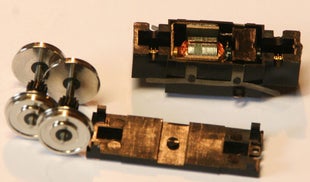
Geopend motordraaistel met oorspronkelijke assen
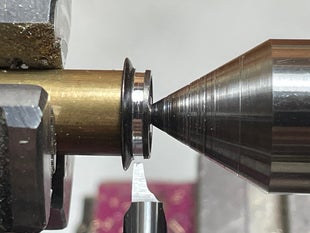
Groef draaien in Märklin wiel
Loop-draaistel
Het tweede, vrij lopende draaistel met zelfde afmetingen als het motordraaistel werd in onderdelen gefreesd uit messing op basis van een ontwerp in Google SketchUp. Er passen twee Märklin assen in.
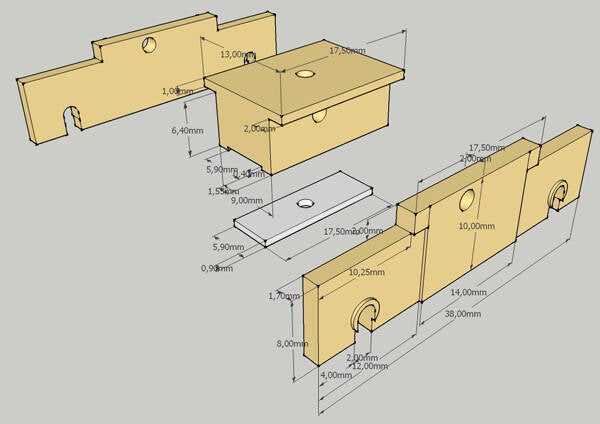
De onderzijde werd ietsje verdiept zodat daarin een sleepcontact past. Hiervoor is een zgn. fluister-sleper van Roco gebruikt (54 mm lange versie). Het rust op een klein plastic plaatje ter isolatie (witte deel in de ontwerptekening). Alle verbindingsboutjes zijn M2, de gaten in het blok zijn 1,8 mm geboord en dan voorzien van schroefdraad met een M2-tap
Hieronder het vrijloop draaistel met contact sleper ondersteboven gefotografeerd.
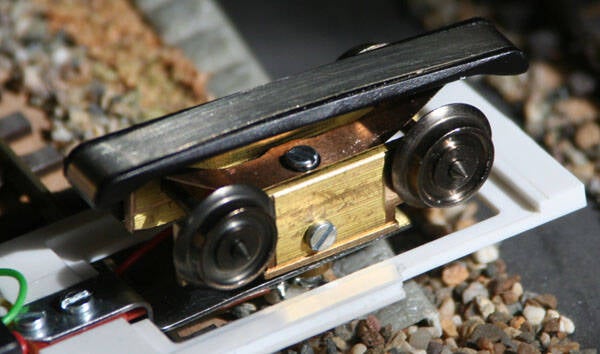
De zijkanten van de draaistellen zijn "gedecoreerd" met imitatie aspotten en veringen. Op de CNC bank werden gestileerde vormen gemaakt die later werden zwart geverfd. Tegenwoordig maak ik dit soort onderdelen via 3D printen waarmee gemakkelijker meer gedetailleerde vormen gemaakt kunnen worden.
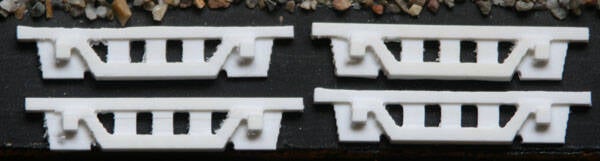
De koppelingen zijn van het type Symoba "Kulissenführung" nr. 111 met daaraan "Schacht Kurz" nr. 110. Deze werden op de juiste plek onder de bodemplaat gelijmd.
De koppelingen zelf die in de schacht gestoken werden zijn van Roco "Profi Kupplung" nr. 40271.
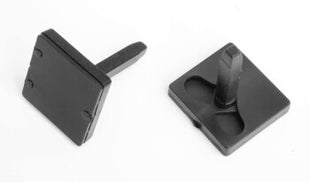
Symoba 111
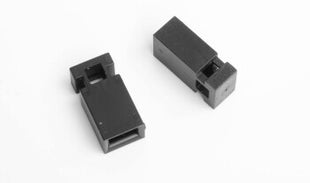
Symoba 110
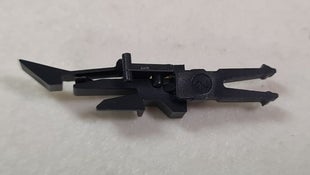
Roco 40271
De buffers werden gedraaid uit PS staf afkomstig van resten uit bouwpakketjes (de "runners" waarvan bouwpakket onderdelen worden afgebroken. In het grootbedrijf werd door de conducteur tijdens de rit overgestapt via een deur aan de voorzijde. Over de buffers lagen stalen platen die als treden dienst deden. Aan voor- en achterzijde werden deze platen opgeklapt.
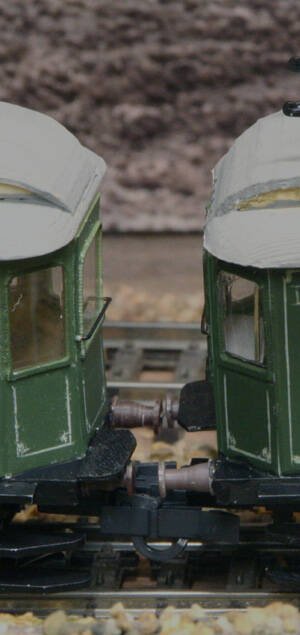
Overstap platen over de buffers neergeklapt
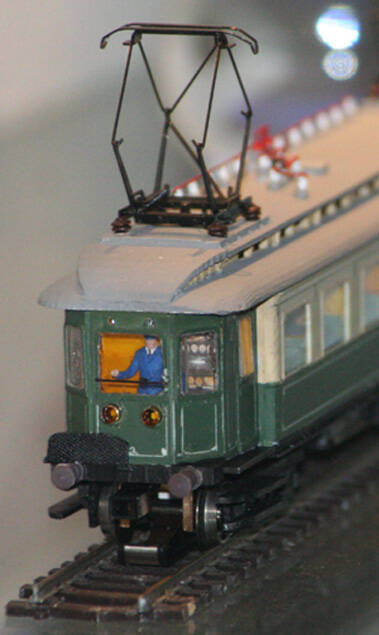
Voorkant met opgeklapte overstap plaat
Bodemplaat
De bodemplaat is CNC gefreesd uit 3 mm dik PS-plaat. Het bevat de draaistellen, de digitale decoder, en een printplaatje met weerstanden voor de verlichting en smoorspoeltjes voor de motor. Alle zijwanden en de binneninrichting met verlichting werden vast gemonteerd op deze bodemplaat.
Hieronder het Google SketchUp ontwerp van de bodemplaat waarvan alleen de onderzijde CNC bewerkt werd. Twee metalen beugeltjes houden de draaistellen op hun plek. Ze zijn achteraf demonteerbaar indien nodig.
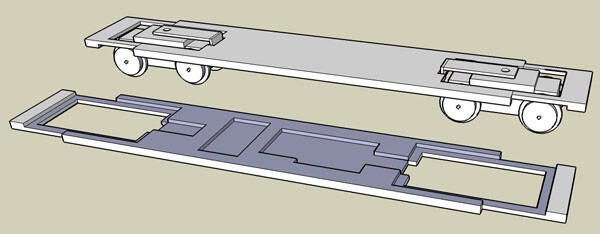
Na monteren van draaistellen, decoder en bedrading ontstond een motorwagen frame dat getest kon worden op rijgedrag.
Het reed perfect, zelfs zonder extra gewicht van de verdere opbouw om de contactsleper aan te drukken passeerde dit kale frame zonder ontsporing over alle wissels en kruisingen
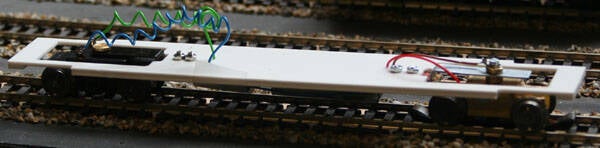
Hieronder: Decoder en bedrading aan onderzijde van het frame
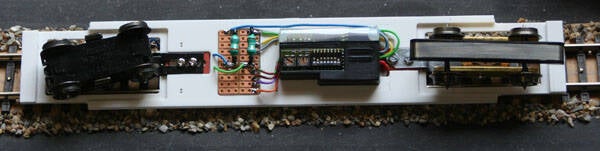
Buitenwanden
Alle wanden werden CNC gefreesd uit 3 mm dik PS-plaat.
Hieronder alle wanddelen na beschilderen en voor montage. Airbrush beschilderd in beige en groen. De witte decoratie werd aangebracht met een kraspen in de groene verf tot aan het witte basis materiaal. De donkere decoratie op het beige stuk is er opgetekend met een potlood. Het geheel is daarna met Airbrush bedekt met een heldere satijn-glans acryl coating.
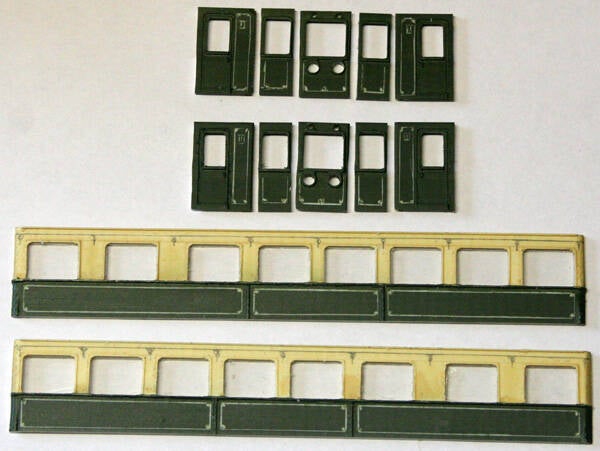
Voor- en achterkant bestaan ieder uit 5 losse delen die als één stuk gefreesd werden en later van elkaar gescheiden (de rode delen in het ontwerp werden er tussenuit gehaald) om vervolgens aan elkaar gelijmd te worden volgens het getekend ontwerp. In deze delen kwamen ook de koplampen (3mm LED met plat afgevijlde voorkant) en achterlichten (2mm rode LEDs).
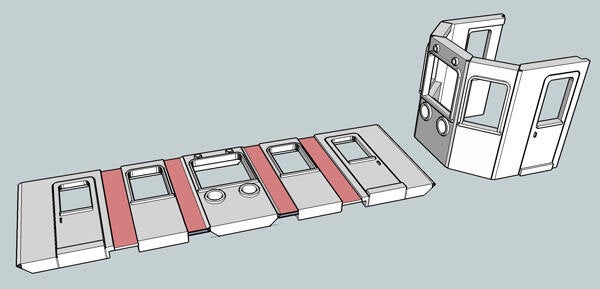
Binnen inrichting en verlichting
De 32 zitbanken hebben allemaal dezelfde vorm maar verschillen in breedte: 12 banken van 9mm breed, 8 banken van 13mm breed and 12 banken van 11mm breed. Ze werden gefreesd uit 6 mm dik plaat met de rugleuningen plat achterover op het feesbed. Zo ontstane lange (in termen van zitbank zeer brede) stroken werden vervolgens ingekort tot de gewenste bank-breedte van 9, 11 of 13mm. Hieronder het ontwerp voor de CNC frees besturing en rechtop als voorbeeld de drie bank afmetingen.
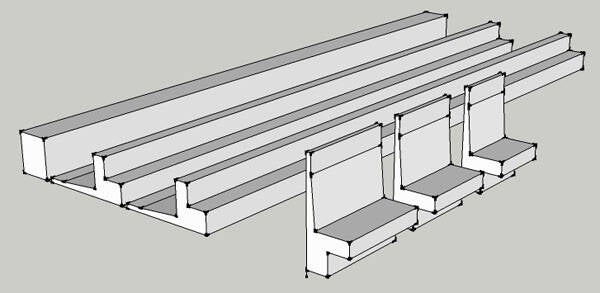
Normaal gesproken wordt binnenverlichting aangebracht als een rijtje LEDs tegen de binnenkant van het dak. Maar het grote voorbeeld toont (foto hieronder links, genomen in het Spoorwegmuseum) hoe op ieder paar rug-aan-rug staande banken een soort schemerlamp staat, een leuke uitdaging om toe te passen in dit model. Dit werd gerealiseerd door het aanbrengen van een witte SMD-LED tussen twee 0,4 mm staaldraadjes (Sommerfeldt) te solderen in de vorm als getekend hieronder in het midden. De draadjes werden tussen twee banken gelijmd en door de bodemplaat gevoerd en en aan de onderkant elektrisch aangesloten. Het boogje bovenop werd doorgeknipt zodat er geen kortsluiting ontstond. Onder rechts het resultaat voor twee nog niet geverfde banken
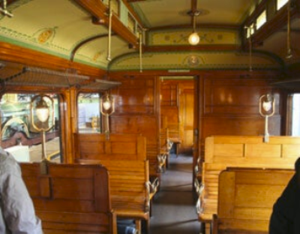
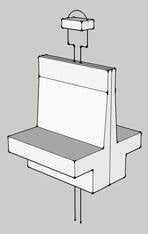
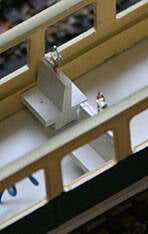
Dak
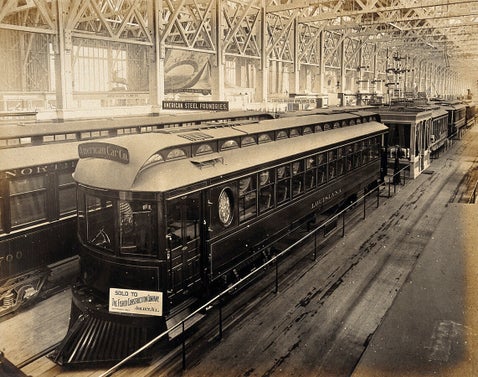
Het dak is van een typisch Amerikaans ontwerp met een verhoogd middendeel dat ruimte geeft voor ventilatievensters. In het boven genoemde boek van J.F.Smit wordt op pag. 25 verwezen naar de St. Louis 1904 wereldtentoonstelling waarvan o.a. dit plaatje te vinden is op Internet.
Het dak van mijn model is opgebouwd uit diverse onderdelen: onderkant, bovenkant, kop-delen, isolatoren voor pantografen en leidingen.
Dak-onderkant
De onderzijde van de dak-onderkant is CNC-gefreesd uit een ABS-plaat van 6mm dik. Als eerste werd de onderzijde gefreesd waarbij de pas-randen bleven staan om het dak precies pas binnen de wagen-wanden te kunnen aanbrengen.
Na omkeren van deze deels gefreesde onderzijde werden de rondingen en openingen van de bovenzijde vorm gegeven.
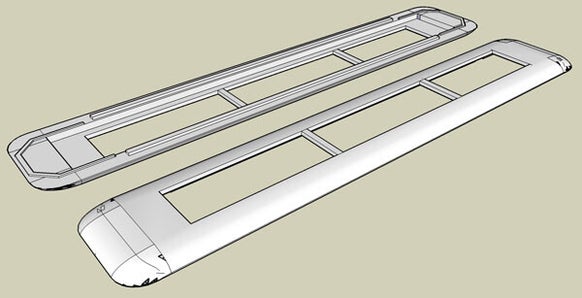
Boven: de onderzijde van de dak-onderkant.
Onder: de bovenzijde van de dak-onderkant
Dak-bovenkant met alle ventilatievensters en pantograaf platforms, eveneens op basis van een 6mm dikke ABS plaat.
Ook dit deel is in twee stappen gefreesd. Dit keer eerst de bovenzijde waarbij ronding en platforms voor de pantografen werden vormgegeven.
Na omkeren op het freesbed werd de onderzijde gefreesd waarbij de stijlen van de ventilatievensters bleven staan.
Hierna werd nog een 2D bewerking uitgevoerd op de bovenzijde waarbij de gaten geboord werden voor pantograaf- en leidingisolatoren. De dimensies voor deze bewerking werden opgenomen in een Excel sheet (een tijdrovend stukje handwerk). De besturingssoftware voor de frees kan Excel data lezen en omzetten in de noodzakelijke bewegingen.
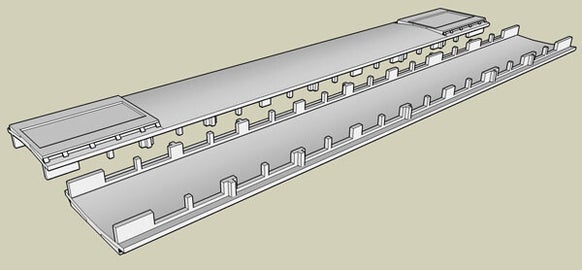
Bove: de bovenzijde van de dak-bovenkant
Onder: de onderzijde van de dak-bovenkant
De kopdelen werden ook weer tweezijdig gefreesd, dit keer uit een 8mm dik ABS-plaatje.
De beide kanten werden gevormd als één stuk en later los gefreesd van het middenblok.
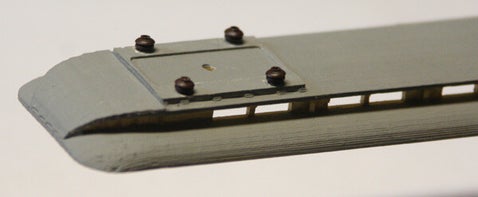
Eenmaal alles gelijmd en geverfd komt het er zo uit te zien.
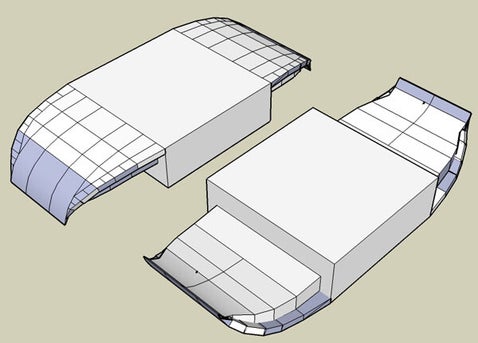
De leidingisolatoren vormen een werkje apart.
Uit een reststukje polystyreen staf uit een bouwpakketje (die staafjes waarvan je de onderdeeltjes moet afbreken) werden isolator modelletjes gedraaid op een kleine tafeldraaibank. De leidingen zijn gemaakt van 0,4mm Sommerfeldt verkoperd staaldraad dat door plaatselijk verwarmen met een soldeerbout (160 gr.C) voorzichtig in de isolatoren werd gedrukt die ter plaatse enigszins smelten en na afkoelen de draden vast houden.
De pantografen zijn van Sommerfeldt artikel #941. Ik vind deze redelijk goed lijken op het origineel al zijn ze eigenlijk gebaseerd op een Duits voorbeeld.

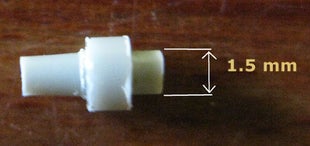
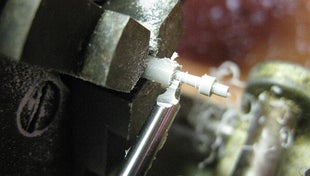
Met zelf-geslepen draaibeiteltje

Het eindresultaat
Plaatjes zeggen meer dan woorden...
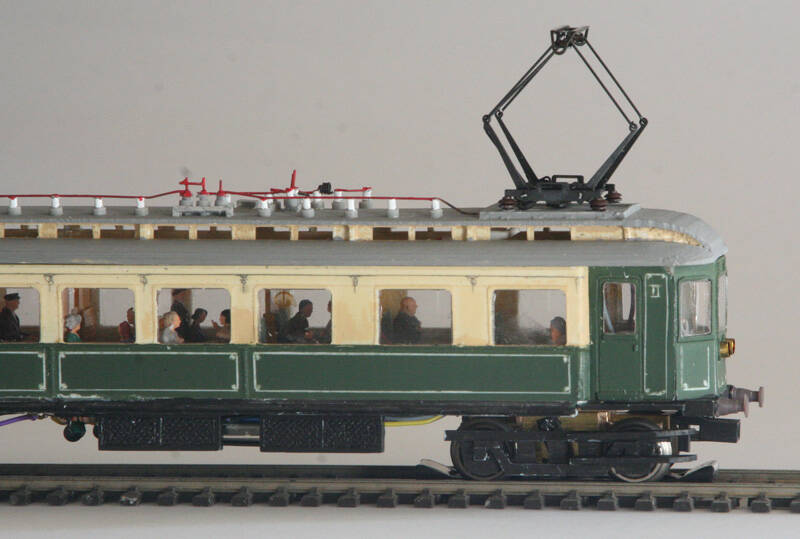
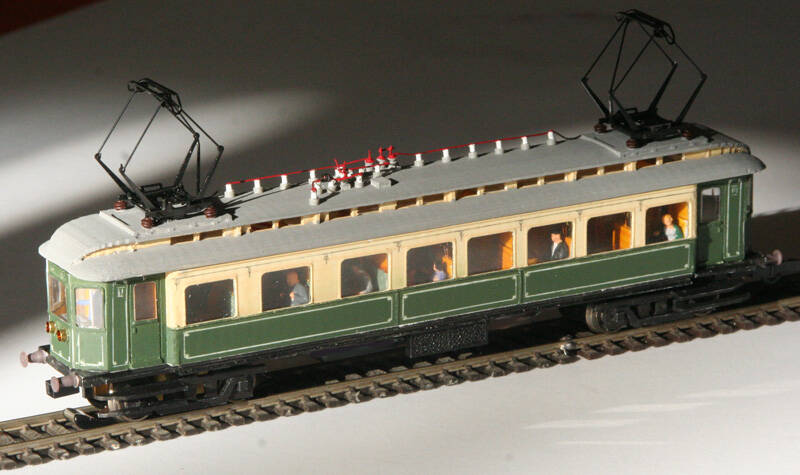
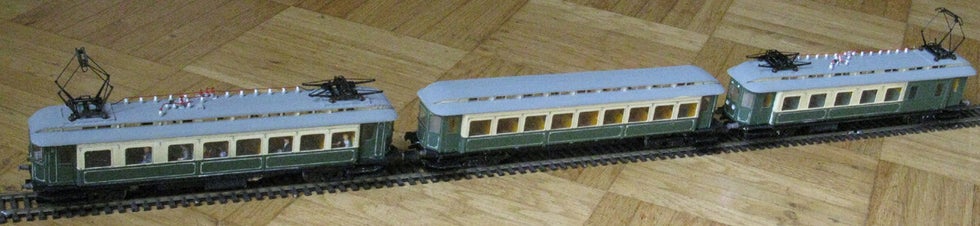
Hier de complete unit. Van links naar rechts mBC (motorwagen, tweede en derde klas (Tenshodo motordraaistel)), C (derde klas wagen) en mBD (motorwagen tweede klas en bagage afdeling, hier nog als dummy motorwagen, inmiddels voorzien van een zelfbouw motordraaistel.)