Project Perronoverkapping
De bouw van dit model werd ook gepubliceerd in "De Modelbouwer" van juni 2023.
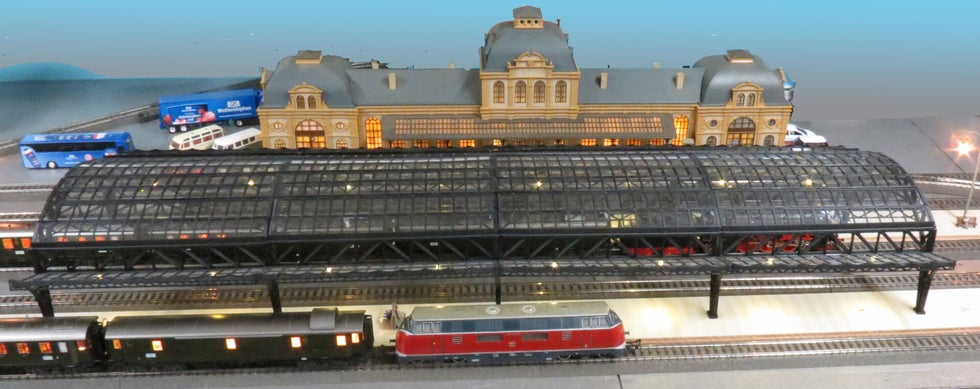
Inleiding
Hier een uitstapje weg van Bank Quay Railway naar de modelbaan van een bevriende relatie. Een grote baan met Märklin C-rails waaraan we samen veel aan de elektronica hebben gesleuteld en ook een perronoverkapping hebben gebouwd van ruim 80 cm lang en 20 cm breed. Alle constructiedelen van deze kap zijn 3D geprint.
Bouwpakketten van perronoverkappingen zijn er in alle soorten en maten, maar om twee redenen hebben we besloten een eigen ontwerp te maken en te realiseren via 3D-printen.
1) Een werkwijze ontwikkelen en uitvoeren om complexe vormen, die gebouwd zijn in een stalen vakwerkvorm, als 3D geprint model te maken.
2)Een eigen maatvoering realiseren, afwijkend van wat standaard geleverd wordt en met een eigen 3D-print ontwerp hadden we daarin natuurlijk alle vrijheid.
Gepland werd een perronoverkapping van één perron naar het volgende, twee sporen overspannend en met luifels aan de buitenzijde van die perrons.
Inspiratie voor de vorm is de constructie van de perronoverkapping van station Weert, weliswaar kleiner dan een sporen-overkappende constructie, maar bijzonder fraai van uitvoering en met de designvrijheid van de modelbouwer zonder meer geschikt om er een omvangrijkere constructie van te maken.
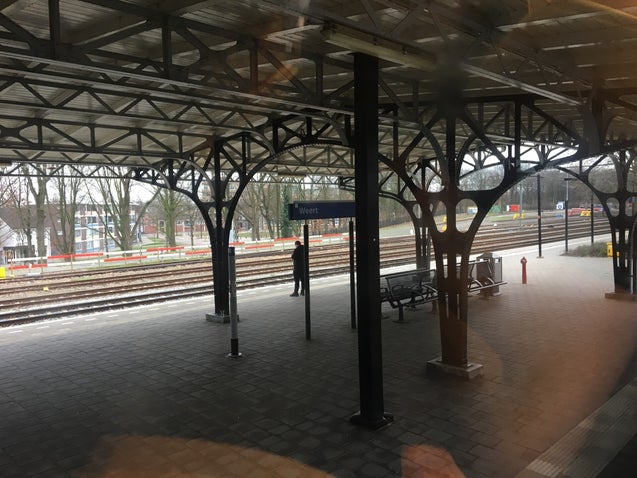
Bouwen met profielen
Er zijn heel wat bouwpakketten te koop van staalbouw constructies als bruggen, kranen, stationsoverkappingen, seinbruggen, bovenleidingsportalen, etc. Voor wie dit soort modellen zelf wil bouwen naar eigen model en/of aangepaste afmetingen zijn er diverse soorten profielen te koop in de vorm van hoekbalken, T-, I-, U of H-balken, buizen, staven (rond, zes-, drie- of rechthoekig). Denk aan in plastic uitgevoerde assortiment verpakkingen of aan de ruime keuze in vormen en maten in messing. Zelfs in hout is e.e.a. te koop en met van dun karton gevouwen L- of U-profielen kunnen ook prachtige constructies gebouwd worden.
Bouwen via 3D-printen
Eerst het 3D-printen van profielen.
Op de 3D-printer wordt de vorm laagje voor laagje opgebouwd, meestal in stapjes van 0,1 tot 0,2 mm. Daarbij moet de eerste laag die op het zgn. printplatform gevormd wordt (0,2 à 0,3 mm dik) dienen om de hele zich daarboven opbouwende vorm stevig vast gehecht te houden aan dat printplatform.
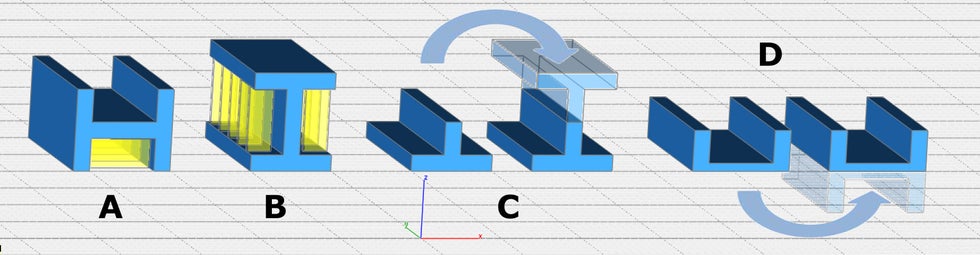
Hoe kan je nu een H-balk printen. Je kan die staand of liggend printen [A, B). Staand hebben we weinig oppervlak om te hechten en moet het hele dwarsstuk ondersteund worden (aangegeven in geel). Liggend is er betere hechting maar moet de hele bovenflens ondersteund worden.
Alternatief is om de H-balk in twee delen te printen en die daarna aan elkaar te lijmen. Één mogelijkheid is om twee T-balken te printen en die met de dunne kanten aan elkaar te lijmen, misschien toch lastig en niet zo stevig [C]. De andere mogelijkheid is om twee U-balken te printen en die met de onderkanten aan elkaar te lijmen, een stuk steviger [D].
Met 3D-printen kan je diverse profielvormen maken en die dan gebruiken om je bouwwerk in elkaar te lijmen maar interessanter is dat met deze techniek meteen ook samengestelde delen van verschillende profielen, in rechte of gebogen vorm, in één keer gemaakt kunnen worden. Heel wat minder werk, mooier qua uiterlijk en veel meer vrijheid in vormgeving.
Daarom nu eerst naar het voorbeeld dat ons inspireerde voor een grote stationsoverkapping, de perronoverkapping van station Weert. Kenmerkend is de opbouw met vooral T-profielen (recht en gebogen) met de bovenflenzen tegen elkaar en in de hoeken versterkt met fraai afgeronde staalplaten
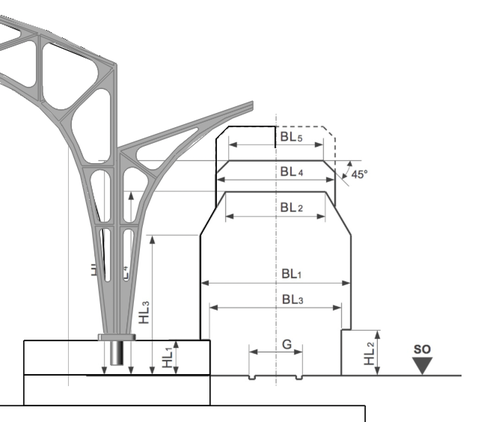
Het te overkappen station bestaat uit twee perrons en vier aangrenzende sporen. De grote kap overspant de twee sporen tussen de perrons, aan de buitenzijde worden de perrons overkapt met een luifel.
Met een eerste idee over de vorm van kap en luifel is de juiste maatvoering gecheckt in relatie tot het zgn. profiel van vrije ruimte waarbinnen treinen zonder hinder kunnen rijden. Met een op schaal aangepaste tekening van dit profiel volgens Morop norm 102 in de projectie van de geplande constructie kan dat goed zichtbaar gemaakt worden.
Meteen is in het ontwerp al te zien wat bedoeld wordt met 3D-geprinte vormgeving. De profielen en versterkende platen met afgeronde hoeken zijn in één keer geprint
Het 3D ontwerp
Als tekenprogramma gebruikte ‘ViaCad Pro 9’ van ‘Punch!CAD’. Inmiddels is dit programma al doorontwikkeld tot versie 15 en is daarbij ook duurder geworden. Voor wie dat toch wat teveel van het goede vindt is de gratis versie van het programma ‘SketchUp’ van ‘Trimble’(v/h Google) een prima alternatief. Het hier besproken ontwerp is daar zonder meer ook goed mee te maken.
Als eerste werd de grote boog tussen de pilaren ontworpen volgens de maatvoering die nodig was voor de aanwezige sporen en perrons, 190mm overspanning en vier keer 205mm afstand tussen de vijf overspanningsbogen.
De luifelondersteuning werd apart vervaardigd en tegen de kap-pilaren gelijmd.
Kap met luifels als één stuk werd te groot voor de 3D-printer.
De afbeelding hiernaast laat de 2D-tekening zien van de boogconstructie, uiteraard maar de helft, de andere helft wordt later eenvoudig door kopiëren, spiegelen en ‘plakken’ toegevoegd.
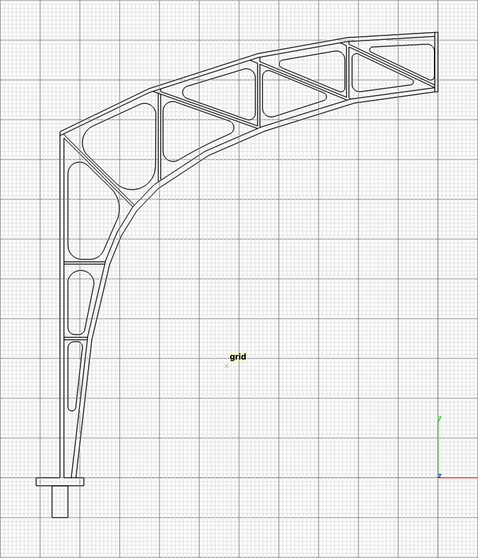
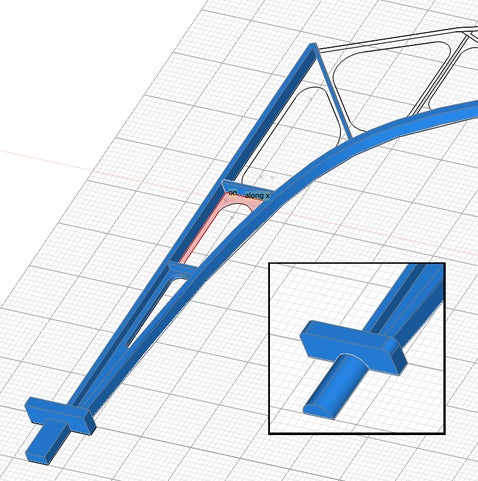
De getekende helft werd tot 3D-vorm gemaakt met het zgn. push-pull-tool. (NB. In andere programma’s is dit meestal ‘extrude’).
De afgeronde staalplaten werden 1mm ‘opgetild’ (in de afbeelding is de onderste plaat al opgetild, die daarboven is geselecteerd voor optillen (rood), de overigen moeten nog).
De L-profielen werden 2,5mm opgetild. Het platte deel van het voetstuk werd 4,5 mm opgetild en de pen daaronder 2 mm.
Met het ’constant blend’ tool werd die pen tot half rond omgevormd (straal 2 mm), de hoeken van de voetplaat werden op deze manier ook afgerond (straal 1mm), zie inzet in de tekening.
De ondersteuning voor de luifels werd op dezelfde manier ontworpen: eerst een 2D-tekening, dan er een 3D-solid van maken met het push-pull-tool. Ook hier werd er één ontworpen en de gespiegelde versie werd verkregen door ‘copy-paste-mirror‘.
In de afbeelding hieronder is het resultaat te zien, in blauw de ontwerpen en in grijs de gespiegelde kopieën. Van ieder van de overspanningsbogen en luifelsteunen werden er twee geprint en vervolgens met de ruggen aan elkaar vastgelijmd. De pennen onder de voetstukken worden daardoor mooi rond (ø4mm). Voor plaatsing op de perrons volstaat het boren van 10 gaten op de juiste plaats.
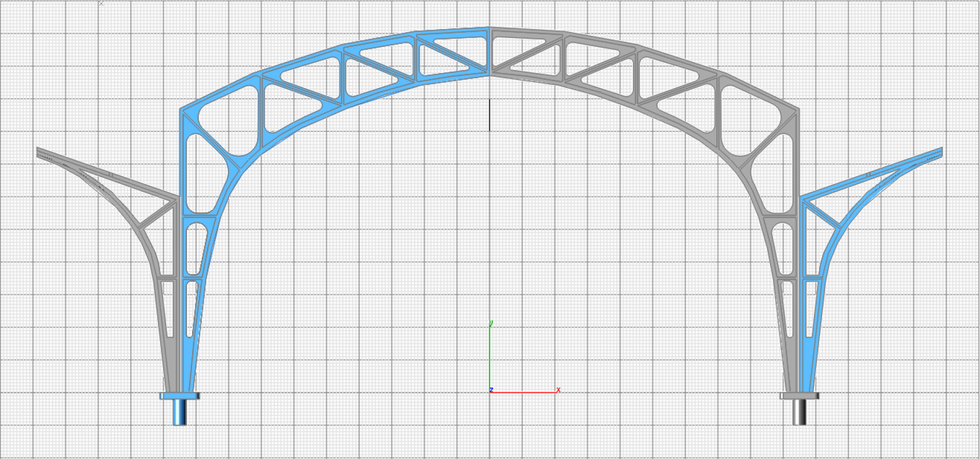
De bogen worden in de lengterichting van de perrons verbonden door een serie lange vakwerkspanten, in totaal 13 stuks in zes verschillende vormen [A-F]
Elk spant werd ook weer voor de halve lengte ontworpen en daarna door ‘copy-paste-mirror’ op lengte gebracht. De spanten A werden rug aan rug op elkaar gelijmd, alle andere werden enkelvoudig gebruikt. Eenzijdig ontbreken van profiel is niet storend, door hun plaats onder de kap is dat nauwelijks zichtbaar. De profielen, met name de bovenranden, werden zo uitgevoerd dat hierin later de beglazing mooi kan worden aangebracht..

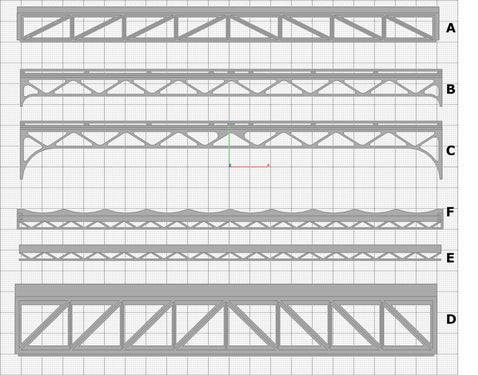
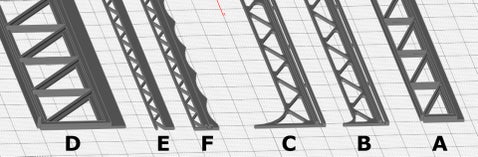
Voor we al deze ontworpen delen gaan printen moet nog een belangrijke verfijning worden aangebracht in het ontwerp waarmee latere montage een stuk makkelijker wordt. Eerst wordt In het tekenprogramma zelf de hele constructie gemonteerd , alle onderdelen in de goede richting en op de juiste plek. Dat hele proces te beschrijven is niet zo zinvol, met een voorbeeld zal blijken welke ontwerp verfijning bedoeld wordt en hoe en waarom dat gedaan wordt.
In afbeelding hiernaast staat een detail van de virtuele montage van de twee eerste rug-aan-rug bogen (blauw en geel) en de daarvandaan lopende dakspanten (grijs). Wat opvalt is dat de spanten en de bogen elkaar op een paar plekken overlappen. Dat betekent voor de echte montage dat er gesneden en gevijld moet worden om het allemaal redelijk passend te krijgen. Met een tool ‘Subtract Solid’ is het eenvoudig mogelijk om van de overlappende gebieden materiaal weg te nemen dat wordt ingenomen door het andere deel. Door dit toe te passen op de overlap tussen boog en dakspant ontstaan inkepingen in de boog waar de dakspanten in passen.
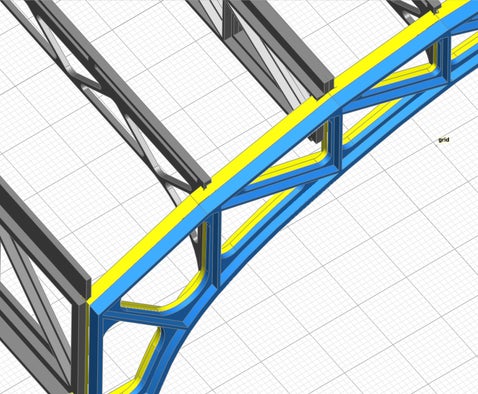
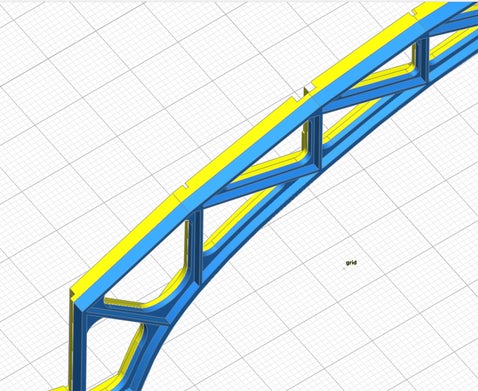
Door dit consequent toe te passen op de hele constructie krijgen we dus twee typen bogen, acht bogen met inkepingen en twee (de buitenste) zonder inkepingen. Hetzelfde geldt voor de luifelsteunen.
We hebben nu dus alle ontwerpen klaar om te gaan printen: 8 bogen en 16 luifelsteunen met inkepingen, 2 bogen en 4 luifelsteunen zonder inkepingen, 24 dakspanten A, en 4 keer 10 dakspanten van resp. spant-type 2xB, 2xC, 2xD, 2xE en 2xF.
Voor we met de printer aan de slag kunnen moeten nog twee ontwerp details uitgewerkt worden: de beglazing en de verlichting.
Beglazing van dak en luifels
De constructie van alle spanten tot zover maakt het mogelijk om in alle openingen, zoals te zien in de virtuele montage hierboven, doorzichtig plastic plaatjes te klikken en vast te lijmen. We gebruikten hiervoor polycarbonaat (PC) plaat van 1mm dik. Plexiglas of polystyreen is waarschijnlijk ook bruikbaar maar zeker meer gevoelig voor breuk dan PC. De uit te snijden (zagen) maten werden bepaald op de 3D-tekening zelf met het ‘tape-measure’ tool.
In werkelijkheid bestaan zulke enorm grote glazen panelen natuurlijk niet uit één stuk. Om een verdeling in kleinere ruiten te simuleren werden op de plaatjes 3D-geprinte ruitverdelingen gelijmd. De ontwerptekening hiervan is hieronder weergegeven.Links de 5 verschillende maten, "opgetild" tot 1 mm dikte en rechts aangebracht in de virtuele montage. Eén serie van 5 maten in rood getekend en die dus in totaal 8 keer werd geprint en aangebracht.
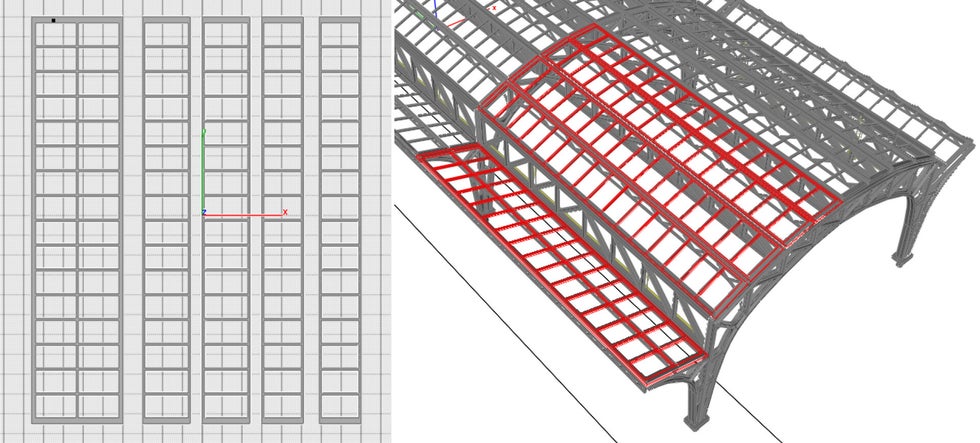
Verlichting
Het handige van 3D-ontwerpen en printen is dat allerlei details zoals de pas-nokjes hierboven of de verlichting integraal vorm gegeven kunnen worden. Als verlichting viel de keuze op Ø3mm warm-witte, opaque LEDs. Door ook een LED in 3D te tekenen in het ontwerpprogramma is het eenvoudig om deze mooi passend in het totaal ontwerp op te nemen. De LEDs werden aangebracht in een 3D-geprinte U-balk die onder de grote spanten tussen de pilaren (type D) werden gelijmd. Per overspanning werden twee LEDs aangebracht, zodanig dat er aan iedere kant acht LEDs op onderling gelijke afstand zitten. De ontwerptekening hieronder laat zien hoe de LEDs in de U-balken werden geplaatst. De lampenkapjes zijn afkomstig uit eerdere projecten en werden gemaakt middels CNC-frezen, dat wordt hier verder niet behandeld. De kapjes kunnen achterwege gelaten worden of anderszins naar eigen idee worden vormgegeven.
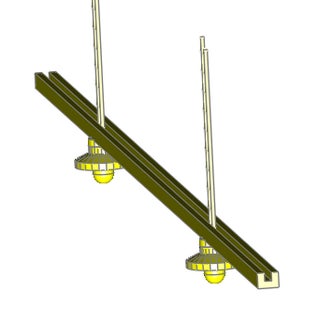
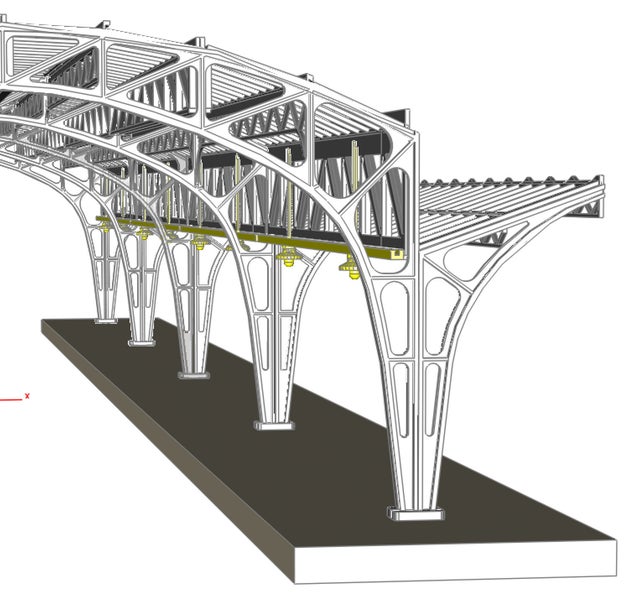
In de afbeelding hiernaast is (in perspectief, allemaal mogelijk in ViaCad) te zien hoe de U-balkjes in de overkapping geplaatst zijn.
Door de plaats van de gaatjes voor de bedrading mee in de 3D-print op te nemen wordt de juiste plaatsing van iedere LED zonder verder te hoeven meten heel makkelijk. Wel eventueel de gaatjes opboren met een 1mm boortje. Na insteken worden de draden naar links en naar rechts tot in de U-balk gebogen. Alle verbindingen werden gemaakt met 0,4 mm verkoperd staaldraad van Sommerfeldt dat goed weggewerkt kon worden in de spantenconstructie.
De LEDs werden aangesloten in vier groepen van steeds vier LEDs in serie, gevoed vanuit het midden en geaard aan de kopse kanten van de overkapping Het schema is hiernaast te zien. De voeding komt van een standaard Märklin transformator die 16 V wisselspanning levert. De vereiste gelijkstroom voor LEDs wordt gemaakt met een eenvoudige eenzijdige gelijkrichting (diode 1N4004) met afvlakkingscondensator. De serieweerstanden begrenzen de stroom op ongeveer 5mA. De LEDs kunnen tot 20mA verdragen, maar bij 5mA geven ze al ruim voldoende prettig licht.
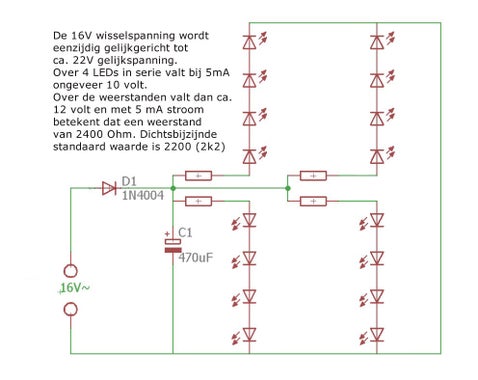
Het resultaat in beeld
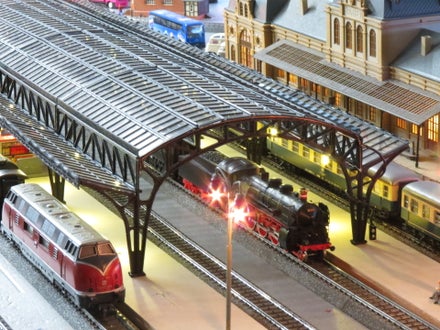
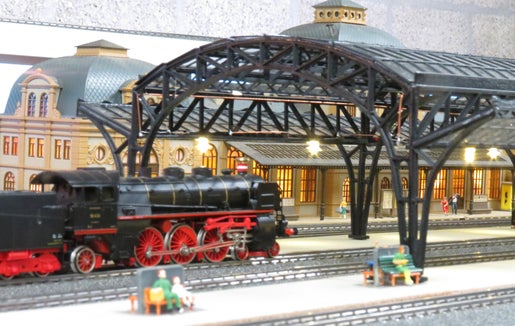
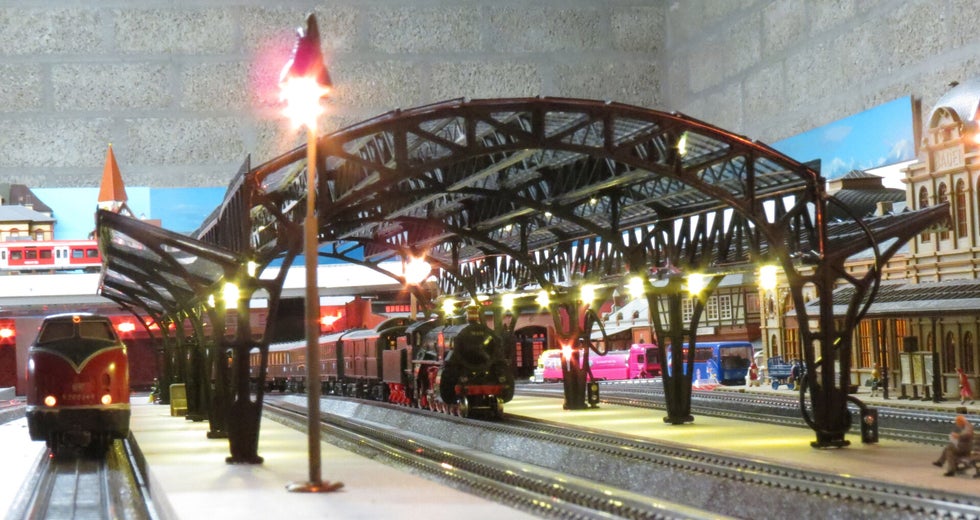
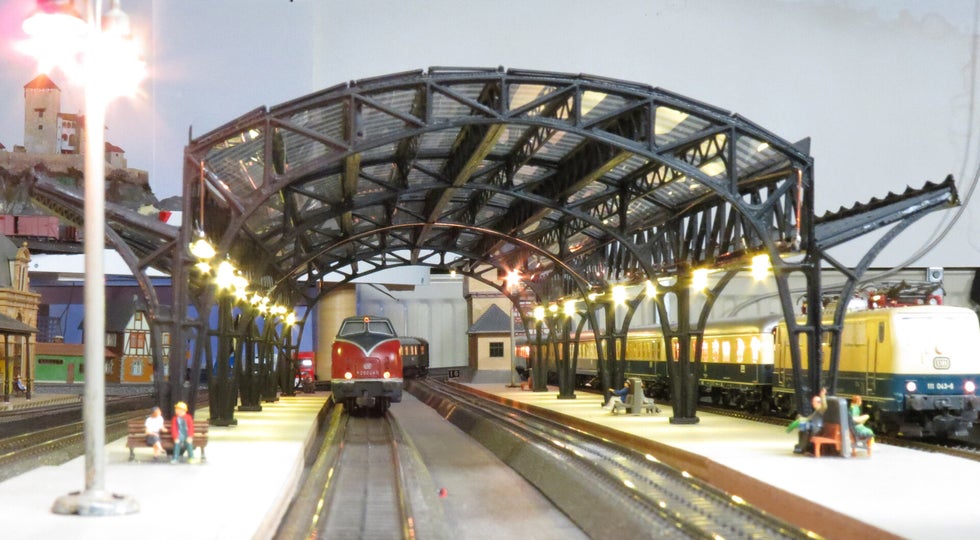
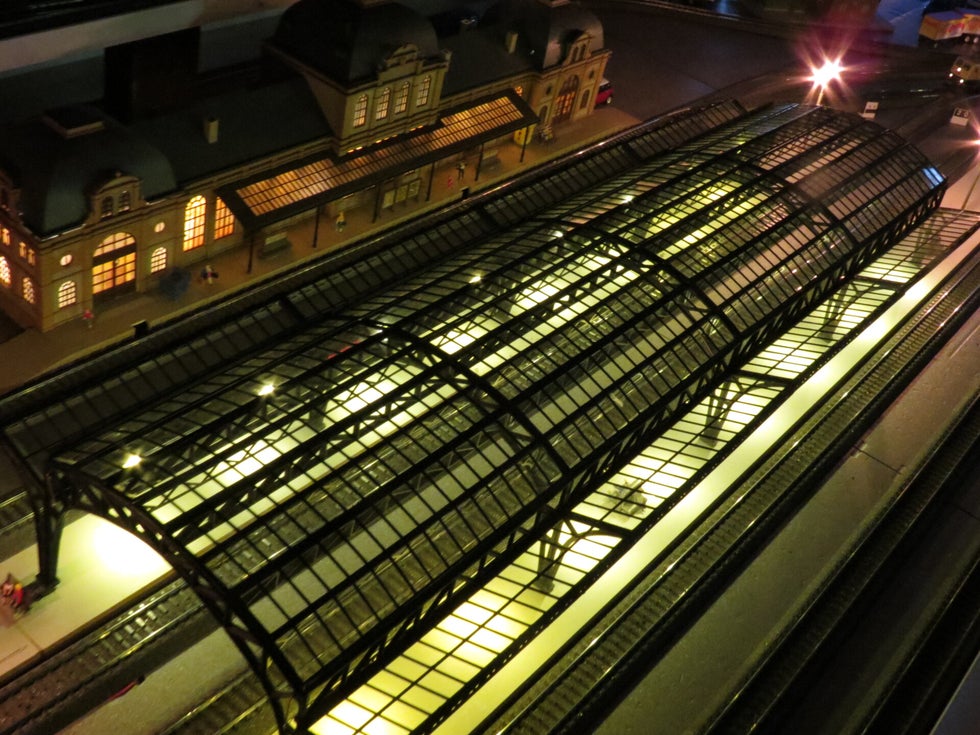